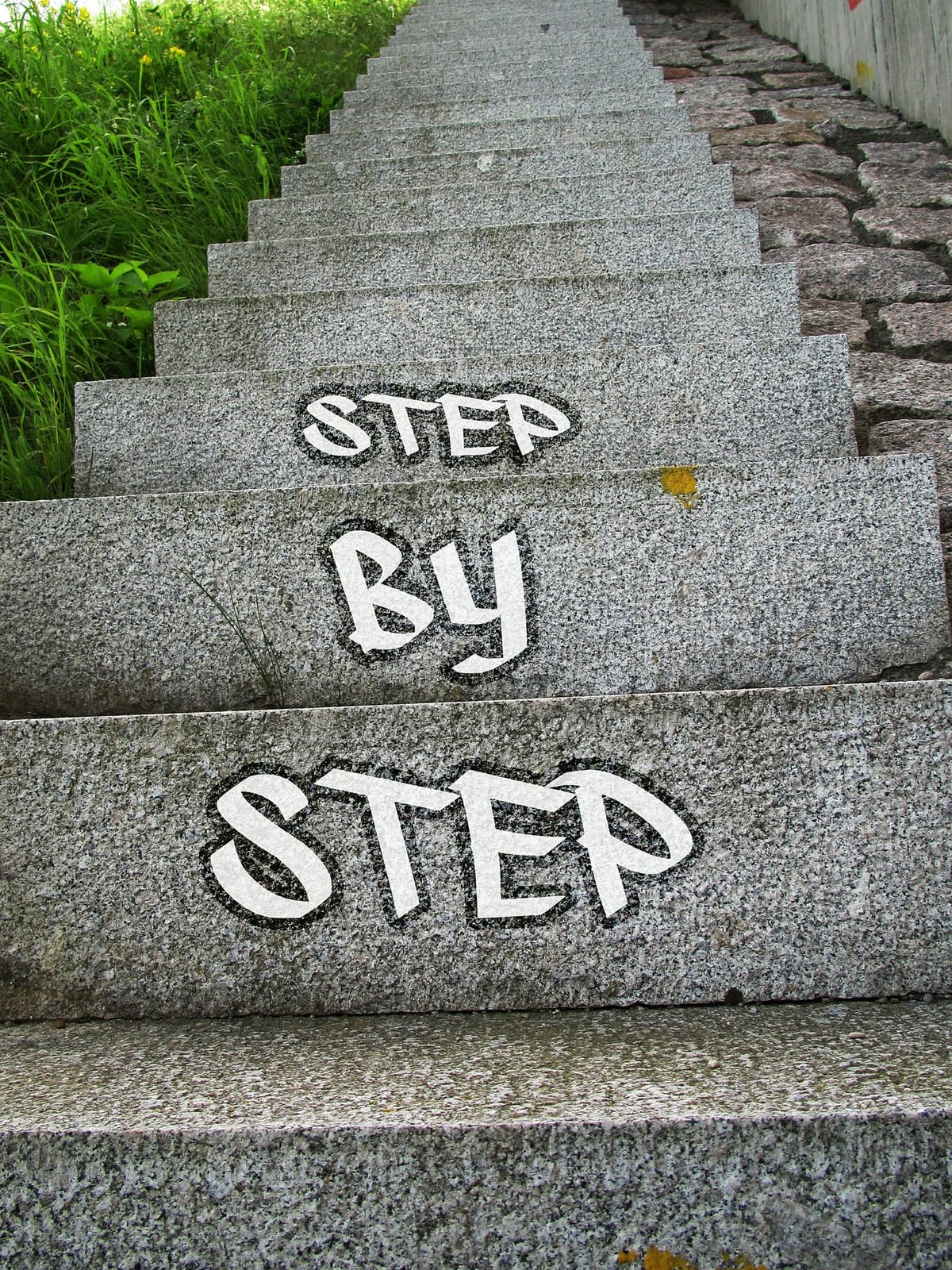
Kaizen, a Japanese term meaning "change for good," embodies the philosophy of continuous improvement through incremental changes and taking a step-by-step approach. It includes the development of management training systems that emphasized the creation of leadership and employee involvement that leads to a culture of continuous improvement. Given the current challenges faced by organizations around productivity losses and increasing operation costs, finding ways to reduce costs is more important than ever to ensure sustainable business growth.
The widespread adoption of Kaizen has resulted in significant successes, driven by both practical tools and a shift in mindset. Kaizen fosters a culture where every individual is committed to ongoing improvement, aiming to create a lean, efficient organization. A continuous improvement mindset is a key Lean principle, which aims to eliminate waste and enhance efficiency. There are two main types of Kaizens: Process Kaizen and Flow/System Kaizen. Process Kaizen involves immediate, small-scale actions to correct defects quickly, often without extensive planning. While effective for quick fixes, it can have unintended consequences if not properly analyzed. Flow Kaizen, implemented at the management level, addresses broader organizational issues with thorough planning, yielding more sustainable results. The choice between these approaches depends on the type of problem being faced.
Common mistakes include using the wrong methodology, leading to frustration and failure. Successful implementation requires the right expertise and commitment. Strategies like Value Stream Mapping, 5 Why analysis, and Fishbone diagrams help identify and eliminate waste, contributing to a more efficient and productive organization.
By understanding and applying Kaizen, organizations can foster the right culture, leading to long-term success and efficiency.
Let's Take Your Business Further. Ask me how.
Dr Kenneth Moodley LinkedIn or www.nikshen.com
Contact: kenneth@nikshen.com
Tags: #Kaizen #Productivity Development #Lean Thinking #Efficiency #Leadership #Kenneth Moodley